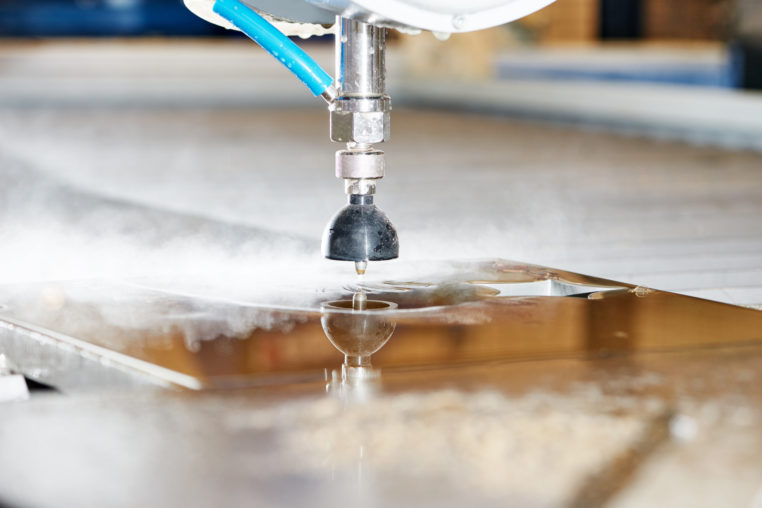
How Accurate is Water Jet Cutting?
Water jet cutting is a technique used to cut through various materials for all your fabricating needs. There are many advantages to using a water jet to cut your materials, but one of the biggest advantages is accuracy. Just how accurate is a water jet, though? Let’s go over the details and discover exactly what a water jet can do for you.
How Does Water Jet Cutting Work?
A water jet utilizes a high-pressure stream of water to erode a stock material to cut it to a specific pattern. There is a wide range of materials that you can use a water jet to cut, including glass, foam, titanium, tool steel, and iron. To generate the necessary pressure, an ultrahigh-pressure water pump is used to create a stream of water that is pressure rated up to 94,000 psi. To put that into perspective, that is approximately 38 times the maximum rated pressure of a fire hose.
The high-pressure system of a water jet consists of a pump, a cutting nozzle, and plumbing. This system is attached to a machine that allows you to cut materials on an X, Y, or Z-axis. The entire water jet is run by a control system with sophisticated programming software, an operator interface, and a velocity feedback system that tells you how much pressure your water jet is producing. Despite the high pressure, a water jet is not rigid, and so it requires the programming software and interfaces to compensate for the lack of rigidity. Otherwise, you could end up with a cut that is extremely precise at the top but becomes less so toward the bottom.
Pure vs. Abrasive Water Jet Cutting
There are two different kinds of water jet operation: pure and abrasive. With pure water jets, the cutting is performed simply with a high-pressure stream of water. This method is perfect for softer materials, such as thin rubber, felt, or paper packing material.
Abrasive water jets use a special nozzle with a vacuum to pull a granular (typically garnet) into a water stream that operates at a higher pressure than pure water jets. The granular element is then mixed with the water, which allows the water jet to cut through harder materials, such as iron, ceramic, glass, and stone.
What Are The Benefits Of Water Jet Cutting?
- No limitations on materials: A water jet can be used to cut through many different materials without concern about damaging equipment or needing to use special tools. This ability means you can swap materials to be cut with little time spent swapping tools between each material, saving time.
- No concerns about heat-affected zones: Unlike lasers, water jets are considered a cold cutting method. So, not only are they able to deliver clean cuts to your materials, but they eliminate the risk of burns to operators.
- No environmental hazards: Water jet cutting does not create any hazardous waste or conditions, such as noxious fumes. It also uses far less energy than a laser cutter or traditional tools.
How Accurate Are Water Jet Cutting Techniques?
When it comes to fabrication, precision is of the utmost importance. Pieces have to fit together perfectly according to individual specs, and sometimes, there is no margin for error in the cutting process. For this reason, a water jet is the perfect cutting tool.
Water jets excel at cutting parts to tolerances as extreme as close to 0.001″ (0.025 mm). And typical water jet cutting projects require materials to be cut to tolerances that range from 0.003″ to 0.005″ (0.076 mm to 0.12 mm). When it comes to materials that are greater than 1 inch thick, a water jet’s accuracy can drop to tolerances with a range of 0.005″ to 0.500″ (0.12 mm to 2.5 mm). Some water jet cutting machines can also allow for angled cutting, which can expand the complexity of parts that you can fabricate with a water jet.
The initial hole made by a water jet in the erosion process can be slightly irregular, particularly when it comes to thicker materials. This is because of the extra effort required to cut through the material for the initial cut. However, once the initial cut has been made, the rest of the lines should be extremely accurate.
The high-quality accuracy of a water jet also means that materials require few if any, finishing processes once they are cut. The fewer processes a material has to go through, the less chance that it will slip below tolerances. And, eliminating finishing processes makes material cutting a quicker and more efficient process.
Accuracy In Parts Tolerances Related To Heat Distortion
Laser cutters are often cited as an alternative to the water jet process because they are also highly precise and leave a smoother edge in the material being cut. However, lasers use high heat to cut through materials, which leaves a radius of heat that extends out from the cut area. This radius can distort the physical properties of the material, warping or even melting it, which can easily affect the finished product. Because a water jet is a cold cutting method, there is no heat distortion to the material, making for a smoother and more precise cut with less waste.
Etching/Partial Cutting Accuracy
The one area where water jets struggle with accuracy is in etching or partially cutting a material to a specific depth. Because of the way water jets work, they achieve their greatest accuracy by cutting entirely through a material all at once. It’s also a challenge to control the timing of a water jet machine’s motion to achieve a properly consistent depth in an etching.
Accuracy Is Just One Part Of Quality Workmanship
When you have a project that requires tight tolerances, or that you just want to be done well, you must turn to an expert to ensure the best possible end result. Water jet cutting is just one of the many tools that AR Iron, LLC, uses to get the job done right. Since 1989, we have provided high-quality ornamental ironwork to the Las Vegas area. We started as a small busin7ess, and even though we’ve expanded to include over 2,000 employees, we’ve kept the heart of a small and dedicated business.
Please contact if you have any questions or need professional-grade ironwork done.