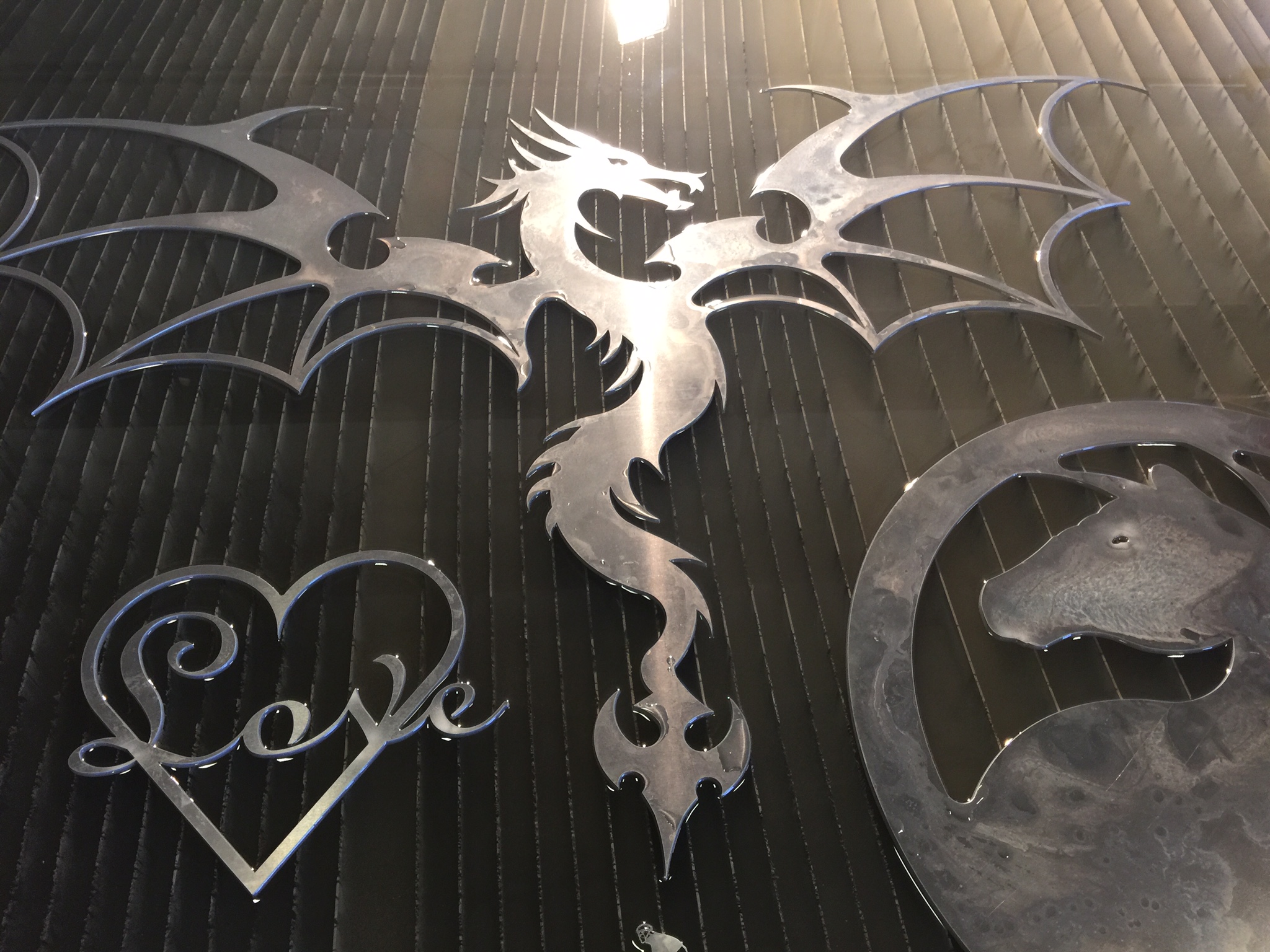
7 Reasons Why You Should Use Waterjet Cutting
There are many applications to waterjet cutting. It is an incredible and precise means of performing precision cutting work on a broad range of materials. From being environmentally friendly to prototyping efficiency, there are a number of reasons why you would choose the use of a waterjet cutter over other forms of precision metal shaping methods. Learn these seven advantages to and reasons why you should choose waterjet cutting the next time you need precision cutting work done.
Waterjet Cutting Creates No Heat
In many cutting applications, too much heat can damage the material you’re cutting. Excess heat can warp, bend and misshape metals like iron and steel, and can utterly destroy plastic. Waterjet cutting creates no heat whatsoever. This means you’ll be able to slice right through the material without the risk of melting, warping or otherwise ruining the project.
No Harmful Dust
With many types of cutting and grinding, the project throws metal shavings, dust and other particulates in the air which are not only unfriendly to the environment, but they can be extremely unsafe and even toxic to breathe. You needn’t worry about this with waterjet cutters, as they produce no particulates or dust whatsoever.
Very Little Waste
With other forms of cutting, you can end up with a lot of wasted material due to large kerf widths, blades and inaccuracy. Waterjets produce very little waste material, meaning it’s an economic savings in the long run.
Prototyping
Waterjet cutters are ideal for the production of prototype parts. It is an exceptionally efficient means of cutting, and the cutter can be programmed with the precise measurements of the part needed. It is faster and just as clean as having parts custom machined.
Ease of Automation
Human error can often be largely removed from the equation for repetitive tasks. Waterjets can be programmed to complete tasks in an automated fashion. This will produce identical parts over and over again.
No Rough Edges
Since waterjets are so smooth and fluid, they don’t create rough edges or burrs. This means you can all but eliminate the need for other machining operations from your process. There is no need for grinding, sanding or otherwise smoothing out the final product.
Lightweight and Energy Saving
Waterjets are extremely lightweight when compared to other forms of cutting technology. When properly mounted, they reduce or eliminate issues that can arise with accelerating or decelerating the cutter. This lightweight equipment also reduces energy costs required to operate and move the piece, which is another money-saving feature of the waterjet process.
These seven points are just a few of the many advantages custom waterjet cutting offers over other forms of cutting and machining methods. If you have a project that you think might benefit from the use of a waterjet cutter, we can help. Check out more information about our waterjet cutting services, and get in touch with us for more information today!