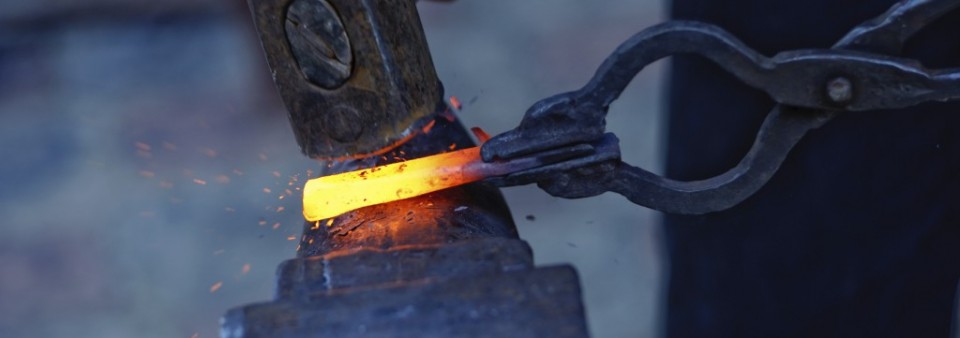
Origin of Decorative Iron
Decorative iron has held a special place in humankind’s achievements ever since its conception. The history of decorative iron follows the history of many of our inventions and structural marvels. Decorative iron has been involved in warfare, the creation of feudal kingdoms, and the erection of tremendous landmarks. Following the past of decorative iron into modern times, we can see this iron in our everyday objects, including chandelier fixtures, wine bottle holders and candlestick supports. AR Iron hopes you’ll enjoy this dive into the origin and background of decorative iron.
What Exactly Is Decorative Iron?
Decorative iron is a form of wrought iron. “Wrought” comes from the past tense of “work,” which makes sense given that this iron has been heavily manipulated by human hands. Previous to the days of steel, wrought iron was the most widely implemented form of iron, and decorations were frequently applied to the iron. Decorative iron consists of lower quantities of carbon than other forms of metal, making it both sturdier and more easily welded.
The Rise of Iron
The advent of decorative iron occurred prior to the Middle Ages in Western history. The iron was created by directly reducing ore deposits, in contraptions known as bloomeries. Around 1104, waterpower was introduced as a means of reducing the ore.
When ore is indirectly reduced, pig iron is created. Pig iron is brittle, however, and it was of little use in terms of constructing hardware. The osmond process came about as a more effective means to indirectly reducing ore. The process, traced back to 1203, became popular in Europe, though bloomery production of iron was still widely used. The osmond process relies on a blast furnace, and historians have uncovered blast furnaces from the medieval time period.
Finery Processes and Puddling
As time progressed, the technologies to create decorative iron advanced. By the 15th century, finery processes were replacing bloomeries and the osmond process. Finery processes occurred in two types—the German version and the Walloon version.
300 years later, in the later 18th century, finery processes were taken over by a technique known as puddling. Puddling involves the use of a puddling furnace, which does not rely on burning charcoal. The ore doesn’t come into contact with the fuel source, and the iron remains uncontaminated by impurities from the fuel burning. The Swedes developed a derivative of this process known as the Lancashire process. These processes are all outdated and obsolete at this point in time, though their history reveals much about the advancement of human technology.
The Bessemer Converter Changed the Game
The American James Aston created a new, more efficient method for creating decorative iron in 1925. With Aston’s process, molten steel is obtained from a Bessemer converter and cooled by liquid slag. The method allowed gases trapped in the metal to escape, creating a more pure iron product. The Bessemer process allowed steel to overtake iron’s role in the world around 1865. Decorative iron was still widely used for aesthetic pleasure, however.
The History of Decorative Iron Has Led Us to the Beauty Created by AR Iron
AR Iron is dedicated to providing beautifully crafted products and superior services to our customers. If you’re in need of decorative iron to enhance the appearance of a structure or construction project, contact AR Iron.