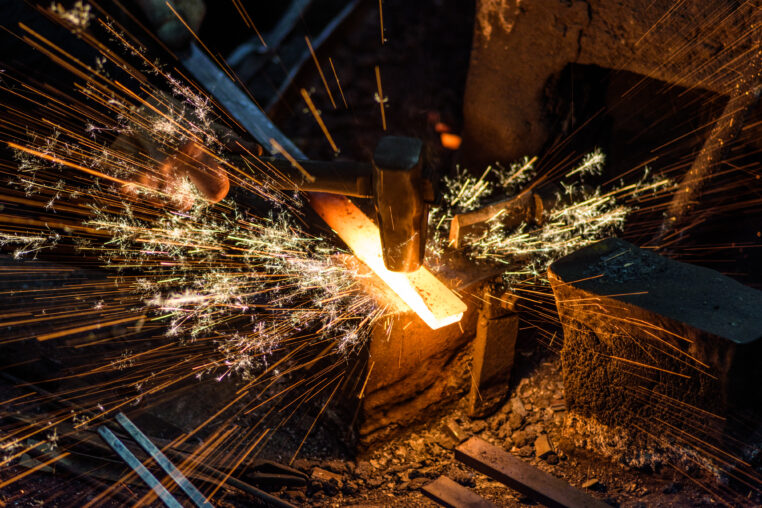
How Iron Forgings Are Made
Iron forging is a process that shapes metal through compressive forces, creating products with increased strength and durability. This technique has been used for centuries, starting with blacksmiths who crafted essential tools and weapons.
Today, it continues to be an important method in modern manufacturing, known for producing high-quality metal parts. Forging refines the internal grain structure of metal, making it more resistant to wear and stress, which is why it remains a preferred method for creating strong, reliable components. From gates and fences to ornamental iron and tools, forged iron products are known for their resilience and long-lasting performance in a variety of applications.
Types of Forging Methods
Impression Die Forging (Closed-Die)
In this process, metal is placed between two specially-shaped molds, or “dies.” When pressure is applied, the metal is squeezed into the shape of the mold. This method is great for creating small, complex parts with precise details. Think of it like using a cookie cutter but for metal. The dies ensure that the final product comes out exactly as designed, making it ideal for industries that need high-quality parts like car or airplane manufacturers.
Open Die Forging
Open die forging is a bit more straightforward. Instead of being fully enclosed in a mold, the metal is pressed between flat surfaces and shaped as needed. This method is often used for simpler or larger items, like big metal shafts or rods. After being shaped, the parts might need extra work, like machining, to get them to the exact size and finish. It’s perfect for making large, strong parts without the need for intricate details.
Rolled Ring Forging
Rolled ring forging is a specialized process used to create circular parts, such as rings. It starts with a donut-shaped piece of metal, which is heated and then rolled out to form a seamless ring. This process strengthens the metal and makes it more reliable by getting rid of internal defects. Rolled rings are commonly used in things like gears, bearings, and other round parts that need to handle a lot of stress without breaking.
Forging Processes by Temperature
Hot Forging
Hot forging involves heating the metal to extremely high temperatures, making it soft and easy to shape. When metal is heated this way, it becomes more ductile, meaning it can be bent or molded without breaking. This process not only allows for easier shaping, but also improves the strength of the metal by refining its internal grain structure. The end result is a stronger, more durable part. Hot forging is commonly used for making parts that need to handle heavy loads, such as in the automotive and construction industries.
Warm Forging
Warm forging is done at temperatures lower than hot forging but still high enough to make the metal easier to work with than at room temperature. This method strikes a balance between the precision of cold forging and the efficiency of hot forging. It’s often used when the metal is already close to its final shape and only needs minor adjustments. Warm forging requires less energy than hot forging, but still allows for good shaping and strength.
Cold Forging
Cold forging, as the name suggests, is done at or near room temperature. This method offers the highest precision, meaning that parts often come out looking very close to the final product without needing much finishing. However, because the metal isn’t heated, it’s tougher to shape, and the process can create internal stresses in the metal, which may lead to issues like cracking over time. Cold forging is ideal for smaller parts that require tight tolerances, such as fasteners and screws.
Steps in the Forging Process
1. Heating the Metal
The first step in the forging process is heating the iron to a specific temperature based on the chosen method. For hot forging, the metal is heated to a high temperature, often above 2,000°F, which softens the iron, making it easier to shape. The heat allows the iron to become more pliable, so it can be molded without cracking or breaking. In warm and cold forging, the temperatures are lower, or the metal may not be heated at all, depending on the requirements.
2. Deforming the Metal
Once the metal reaches the right temperature, it’s time to shape it. This is done using heavy machinery like dies or hammers. Dies are molds that press into the metal with high force, giving it the desired shape. In some cases, a hammer is used to pound the iron into shape, especially in open die forging, where the metal is worked manually. This part of the process ensures that the metal takes on the exact form needed for the final product.
3. Cooling and Finishing
After the metal has been shaped, it needs to cool down. During this cooling phase, the iron hardens and solidifies in its new form. Once cooled, finishing touches are added to the piece. This can include trimming off any excess material (called flash), polishing the surface, or applying treatments to protect the metal from rust and wear. These finishing steps ensure that the final product is smooth, durable, and ready for use.
Forging vs. Other Manufacturing Methods
Forging vs. Casting
Forging and casting are both popular methods for shaping metal, but they differ in key ways. In forging, metal is shaped by applying pressure, which helps refine its internal structure, making it stronger and more durable. This process creates parts with superior strength compared to casting, where metal is melted and poured into a mold to cool.
Cast parts, while often more detailed, can sometimes have internal defects like voids or weak points due to the cooling process. Forging also typically results in better grain structure, which improves the overall durability of the part. While casting may be less expensive for complex shapes, forging is often more cost-effective for high-strength parts that need to handle heavy loads or impacts.
Forging vs. Machining:
When comparing forging to machining, forging often comes out on top in terms of material efficiency. Machining involves cutting away material from a solid block to get the desired shape, which can lead to significant waste. In contrast, forging shapes the metal with minimal waste by using compressive forces.
Additionally, the grain flow of forged parts follows the shape of the piece, giving it superior strength compared to machined parts, which may have disrupted grain patterns due to the cutting process. This makes forging the preferred method for parts that need to withstand high stress, like engine components or structural supports.
Custom Iron Forging: Durable Solutions for Gates, Railings, and DIY Projects
Iron forging has been essential for centuries, known for producing strong, long-lasting parts used in gates, fences, and tools. The process refines the internal structure of metal, making it more resistant to wear and stress compared to other methods like casting or machining.
At AR Iron, we offer custom hand-forgings such as iron balusters, baskets, scrolls, and more, perfect for wrought iron railings and gates—or your own DIY projects! Whether for strength or aesthetic appeal, iron forging remains the go-to choice for high-quality metalwork.