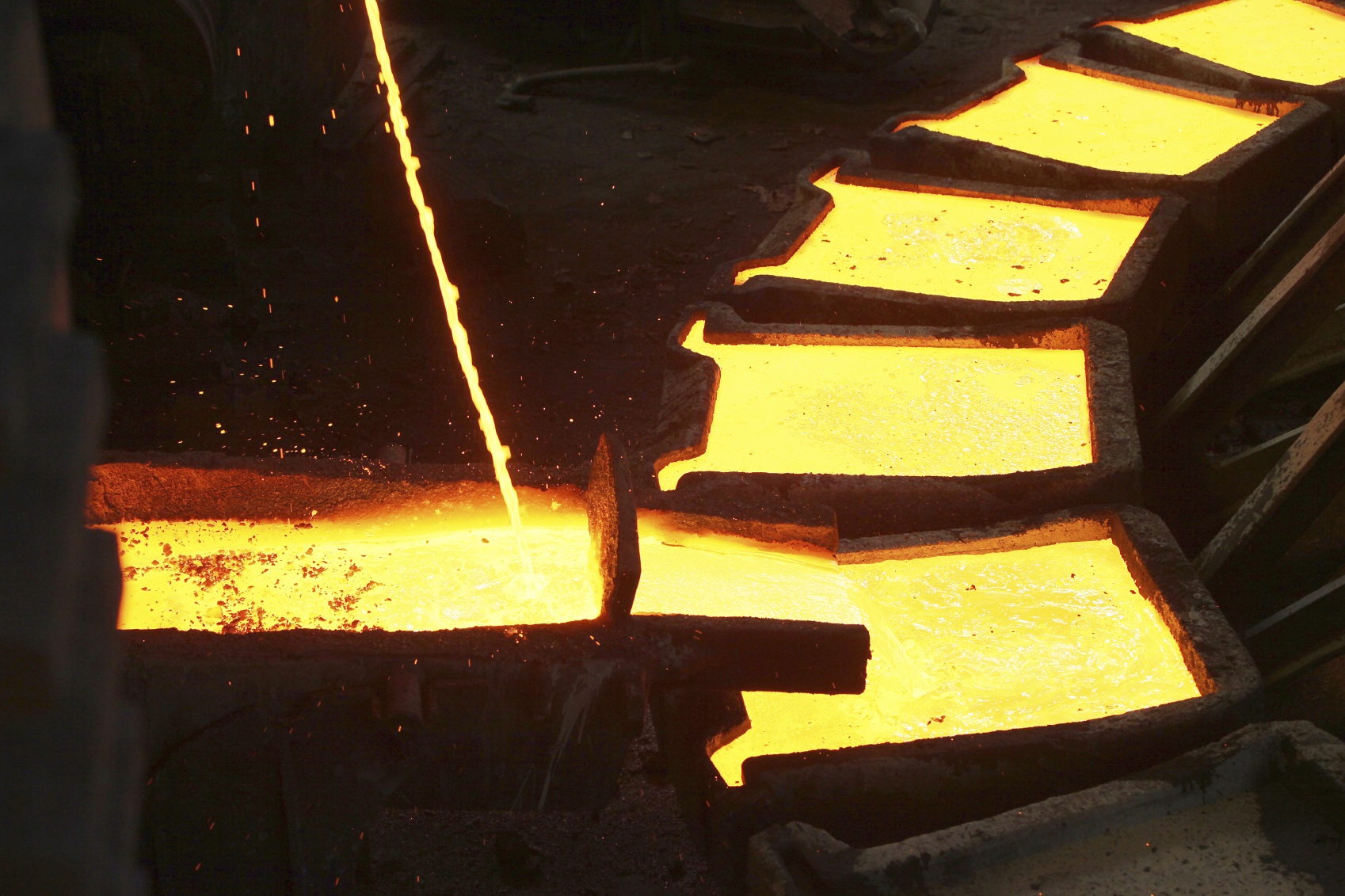
Forging vs. Casting: Which is Better?
When it comes to metal work, there is one question that is asked again and again: Which is better, forging or casting? If you’re considering a big metal working project, then the first thing that you have to decide is which technique you’ll use to complete the job. Because casting and forging both offer distinctive advantages, it’s important to examine each process more closely so that you can know which strategy is right for you.
Fortunately, with the right information, you’ll be easily able to choose between forging and casting so that you can easily complete your project. Learn whether casting or custom forging is the better technique and which one you should use for your next important metal working job.
Casting
Anyone that thinks of metal work most likely conjures an image of casting in their mind. Through the process of casting, a metal material is heated to its melting point and then the molten metal is poured into a mold or cast so that it can take on a new shape. Now that you know a little more about the casting process, it’s time to look at its advantages.
The biggest benefit of choosing casting for your project is that it is very quick and simple, with only melting the metal and pouring it into the cast needed for completion. However, the drawback is that you will need a pre-existing cast for whatever project you’re attempting, limiting your creative possibilities.
Forging
Forging is one of the most versatile options for metalworking that there is, and provides for a high level of flexibility in what you can make in your project. Instead of melting metal as with casting, forging uses metal that has been heated to the point of pliability and can then be reshaped into countless different designs.
Besides allowing you to choose from almost an unlimited amount of designs, the biggest advantage of choosing forging for your project is that it preserves the integrity of the metal to a much larger degree, limiting long term damage and better preserving its appearance over time.
Which is Right for You?
After learning more about these two different styles of metal working, it’s time to decide whether custom forging or casting is the better choice. As previously mentioned, if speed is a factor in your project, then casting is probably the better solution. However, if you’re looking for a higher quality project that will last over time, then the only choice for you is custom forging.
Choosing custom forging means getting exactly the metal product you need that will look great for years to come the way that you want.
Schedule Your Custom Forging Project
When you’re ready to start your custom forging project, you need to make sure that you work with a trusted company that has the experience necessary to complete the job. For quality custom forgings with quick turnarounds, you need to partner with AR Iron, LLC today.
The team at AR Iron will listen to your needs for your forging project and will complete the job quickly and effectively. Contact us today to learn more about our metal working services.