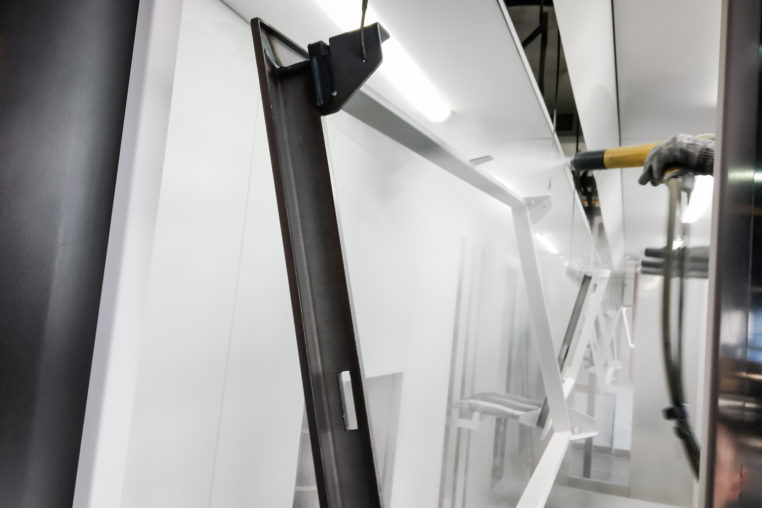
What is the Importance of Pretreatment for Powder Coating
A perfect powder coating is dependent on a metal surface that has been well prepared. Pretreatment is a prerequisite for powder coating of any metallic exterior. This is because various metal surfaces are often pre-coated with dirt or oil that prevents perfect coating of the surfaces. A perfectly coated surface is good for business, for both the customer and the business owner.
However, you may be wondering what the pretreatment process is? It can be defined as the process of chemical preparation of different types of aluminum and metal before applying a powder-coated surface finish. Thus, pretreatment is crucial for ensuring long-lasting results in all cases of powder coating. This article briefly discusses the importance of pretreatment for powder coating and various stages of the pretreatment process.
Why is Pretreatment a Critical Process?
While many people think that a thorough cleaning is enough for excellent powder coating results, pretreatment ensures that the entire finishing process is the best. As mentioned, pretreatment is a process that precedes the actual powder coating of any metal or aluminum surface. The primary importance of the pretreatment process is that it creates a surface that the coating can perfectly adhere to, whether it is a liquid or powder.
Pretreatment significantly heightens the performance of powder coating, whose purpose is to provide excellent protection to the metal being used. Pretreatment also ensures that powder coating reduces a metal’s susceptibility to rust, corrosion, or damage, increasing its use and lifespan. This process also helps the powder coating bond more effectively to create an elegant surface finish, thereby preventing weathering and rusting before the entire powder coating process occurs. Therefore, it is imperative to do the pretreatment process correctly to ensure that the powder coating lasts and functions appropriately.
What are the Pretreatment Steps?
Before the powder coating process, one must follow various steps to ensure the correct pretreatment process of metal surfaces. These steps must be adhered to strictly to enable powder coating bond effectively and perform its purposes efficiently. Below are the necessary pretreatment steps that must be followed for efficient powder coating results:
Cleaner
It is the initial and most crucial stage in the pretreatment process; hence it must be conducted. The quality of the finished part of the powder coating is likely to be poor if it is not entirely cleaned through this stage. The cleaners used are alkaline and contain surfactants to lower surface tension. Cleaner solution concentration and temperature are regulated at this stage to get desirable results. It is important to note that this stage’s normal dwell cycle is usually 90 seconds. Also, the drain zones are always long enough to ensure that cleaning solutions are not carried to the next cycle and are short of ensuring that the cleaned parts do not dry before entering the next stage.
Cleaner Rinse
It’s the immediate stage following the cleaner stage, involving an overflowing clean water rinse. Note that this stage is operated at the same temperatures as the cleaner stage to ensure desirable results. However, the alkalinity level of this stage is limited to only three percent of the cleaner solution concentration to prevent alkaline carry-over to the next acidic step.
Phosphate
Typically, two generic types of phosphate are used in the pretreatment process: iron phosphate and zinc phosphate. From an economic viewpoint, iron phosphates are the best since they are affordable, have few maintenance requirements, and are easier to control. However, this type of phosphate is not recommended when high-quality end products are desired. Conversely, when adequately maintained, crystalline zinc phosphate provides excellent substrates for adhesion, surface appearance, corrosion resistance, and detergent resistance. Unfortunately, zinc phosphate provides poor flexibility for iron phosphate parts, thus requiring thickness to acquire equal gloss. However, regardless of the phosphate used, one must regulate the chemistry and temperature of the solution used. Due to the formation of sludges by these two phosphates, there is a need for regular clean-out of the tanks and spray piping.
Rinse
Like after the cleaner stage, there is a rinse stage after the phosphate stage, and it involves overflowing clean water rinse. The temperature used here corresponds with the one used at the phosphate stage. Its concentration is limited to one percent of the phosphate tank concentration to prevent contamination of passivation solution in the next step.
Passivation Rinse
Improving the overall performance of the metal surface being pretreated involves the passivation of the phosphate surface with chromic acid. The chromic rinses serve the following purposes: (1) dissolution of any water-soluble salts in the pores of the phosphate coating or their conversion into insoluble water salts; (2) improvement of salt spray resistance by coating the surface with soluble chromate and; (3) formation of a thin oxide film in all pores of the phosphate coating. Thus, there is an excellent need for pH control at this stage. Importantly, follow the chemical supplier’s instructions to ensure correct dumping and recharging at this stage.
Final Rinse
It involves three types of rinses; the first rinse involves the use of cold-tap water to rinse the surface after passivation. It is followed by an overflowing and recirculating D.I rinse whose water has been passed through an ion-exchange column to remove all water-soluble salts. It is then followed by a short drain time and a final fresh overflowing D.I rinse. The specific water resistance is the correct measure of removing all water-soluble salts.
Dry-off Stage
The temperature and time for dry-off depend on the pretreatment and the shape of the part being dried. There are additional requirements for changing crystal structure for iron phosphate parts, which improves corrosion resistance. Ordinarily, a metal temperature of 350 degrees F is sufficient for dehydration. A temperature of 400 degrees F is not suitable for both phosphates as it is likely to deteriorate pretreatment. A perfect dry-off process exhibits parts with an ideal uniform surface appearance. The presence of any streaks or splotches leads to the low durability of the powder coating.
Contact AR IRON Today
Are you in Henderson, Nevada, and looking for media blasting and powder coating services? AR Iron LLC is a family-owned business that provides these services alongside ornamental iron, security fences, and security doors in the Las Vegas region. Contact Us today for the highest quality ironworking services in Nevada, or visit our website for more information about our service.